FDM Printing Paths Optimization
Optimization of toolpaths in Fused Deposition Modeling (FDM) 3D printing significantly boosts part strength and stiffness by strategically aligning filaments based on anisotropic properties and structural requirements
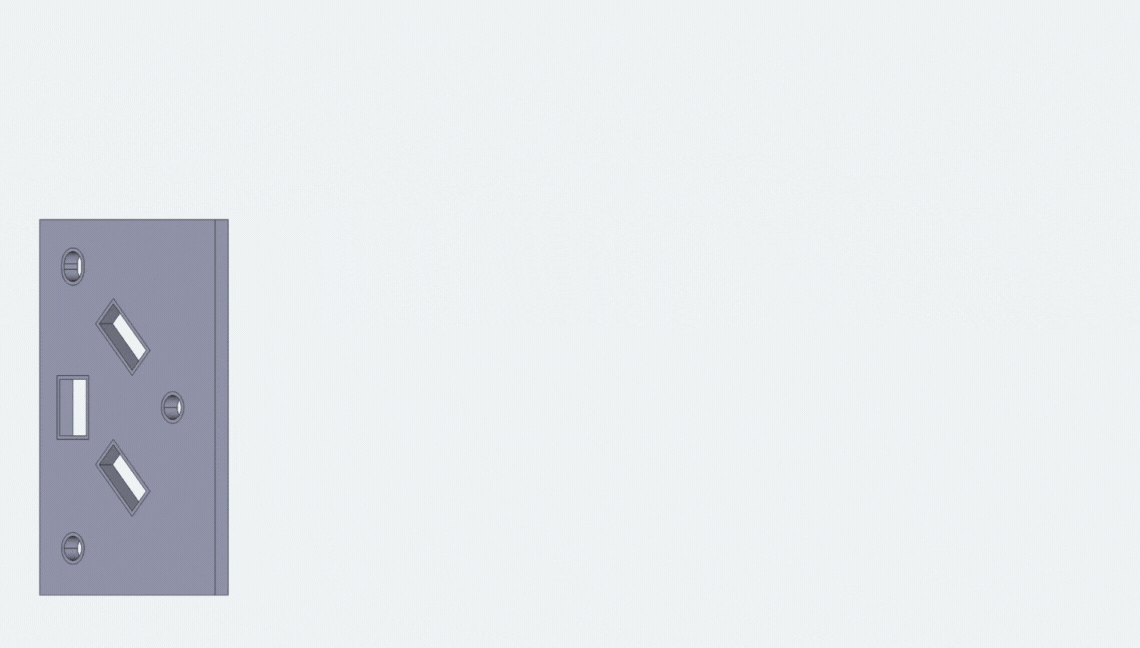
Why Toolpaths Optimization?
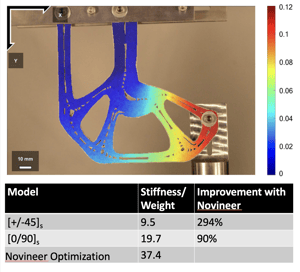
Fused Deposition Modeling (FDM) 3D printing revolutionizes manufacturing by enabling precise control over the filament path within an object. This capability allows us to harness the anisotropic stiffness and strength of the filaments, strategically and spatially placing the filaments based on structure performance and manufacturing specifications. Utilizing FDM technology, we can exploit these anisotropic properties to create toolpaths that optimize load distribution across the structure. Our research studies have demonstrated that optimized toolpaths can increase a part’s specific stiffness and strength by 90% [Ref1]. This optimization marks a significant shift in toolpath design—from being solely 3D printing process-driven to being strategically engineered for maximum structural performance. The implications of such a toolpaths design process extend beyond mere mechanical performance; it redefines what is possible in terms of geometric complexity and material utilization, pushing the boundaries of traditional manufacturing paradigms.
How Novineer Optimizes Toolpaths?
Novineer specializes in both simultaneous topology and toolpath optimization as well as standalone toolpath optimization for pre-defined models. This study focuses on the latter. For any given model, the required inputs include the CAD model, printing specifications, boundary conditions, and material properties. Novineer’s approach begins by determining the printing layers through an analysis of stress gradients. Within each layer, load paths are established based on equilibrium equations. The stresses are expressed in terms of load functions, and the load flow is calculated using the gradient of these functions [Ref2] [Ref3]. From there, regions of major stress are pinpointed, and the toolpaths are aligned along the critical load paths. In less critical areas, known as minor regions, the principal stress directions are identified, and the toolpaths are aligned accordingly to support the overall structural integrity.
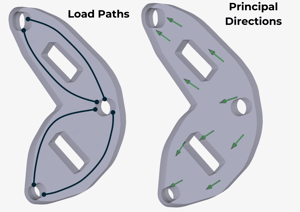
Novineer’s Paradigm-shifting Generative Toolpaths Design
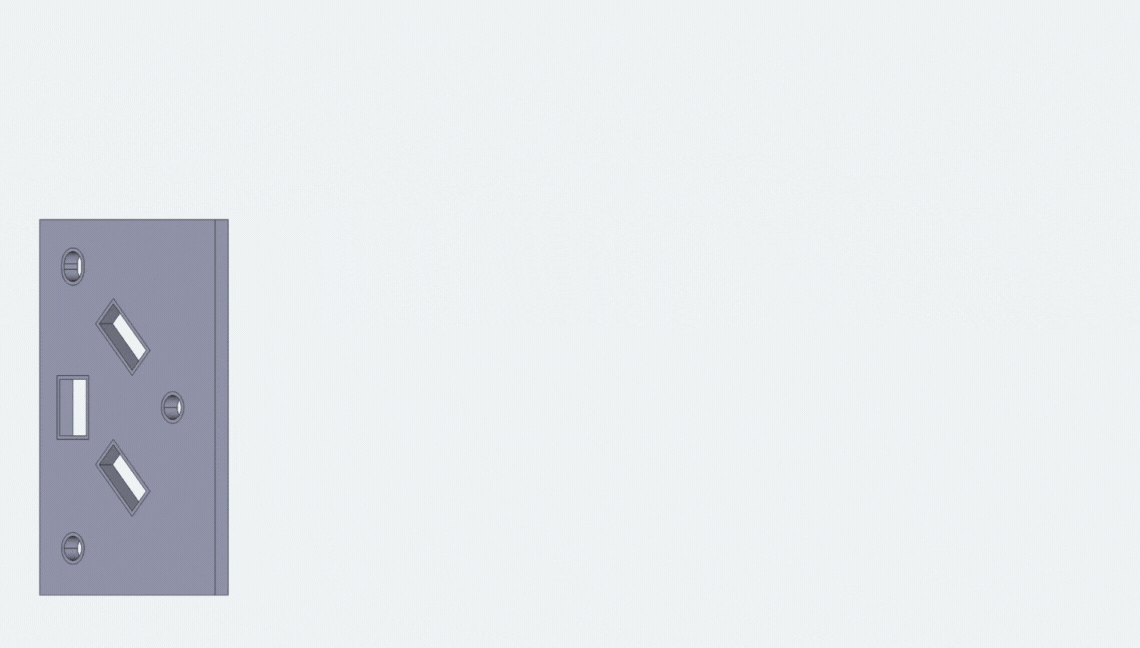
The methodology detailed in the previous section is concurrently executed across multiple layers. Each layer's load paths and optimized principal directions are tailored to fulfill both mechanical stiffness requirements and the constraints of 3D printing. Novineer's dual objectives are: (1) empowering engineers to regain control over the design process and saving their time, and (2) maximizing the potential of 3D printing by enhancing the performance of the parts produced. The toolpaths optimization mirrors Novineer's generative geometric design, which provides editable, optimized geometry. Similarly, the optimized toolpaths are fully editable, enabling users to swiftly adjust the loads, boundary conditions, and printing specifications to immediately observe alterations in the toolpaths. Users can also modify the principal directions to reshape the toolpaths. Ultimately, they receive .iges files for the toolpaths of each layer, which can be modified further using their CAD software, offering a flexible and dynamic design-to-production workflow.